Our wide range of industrial gasketed plate heat exchangers is suitable for all types of industry and multiple applications from heating, cooling and heat recovery to condensation and evaporation. We are constantly looking to extend and upgrade the range, adding new performance criteria and greater flexibility. What’s termed ‘next-generation’ today will soon be standard for the entire Alfa Laval Industrial line.
- Home /
- Industrial line
Industrial line
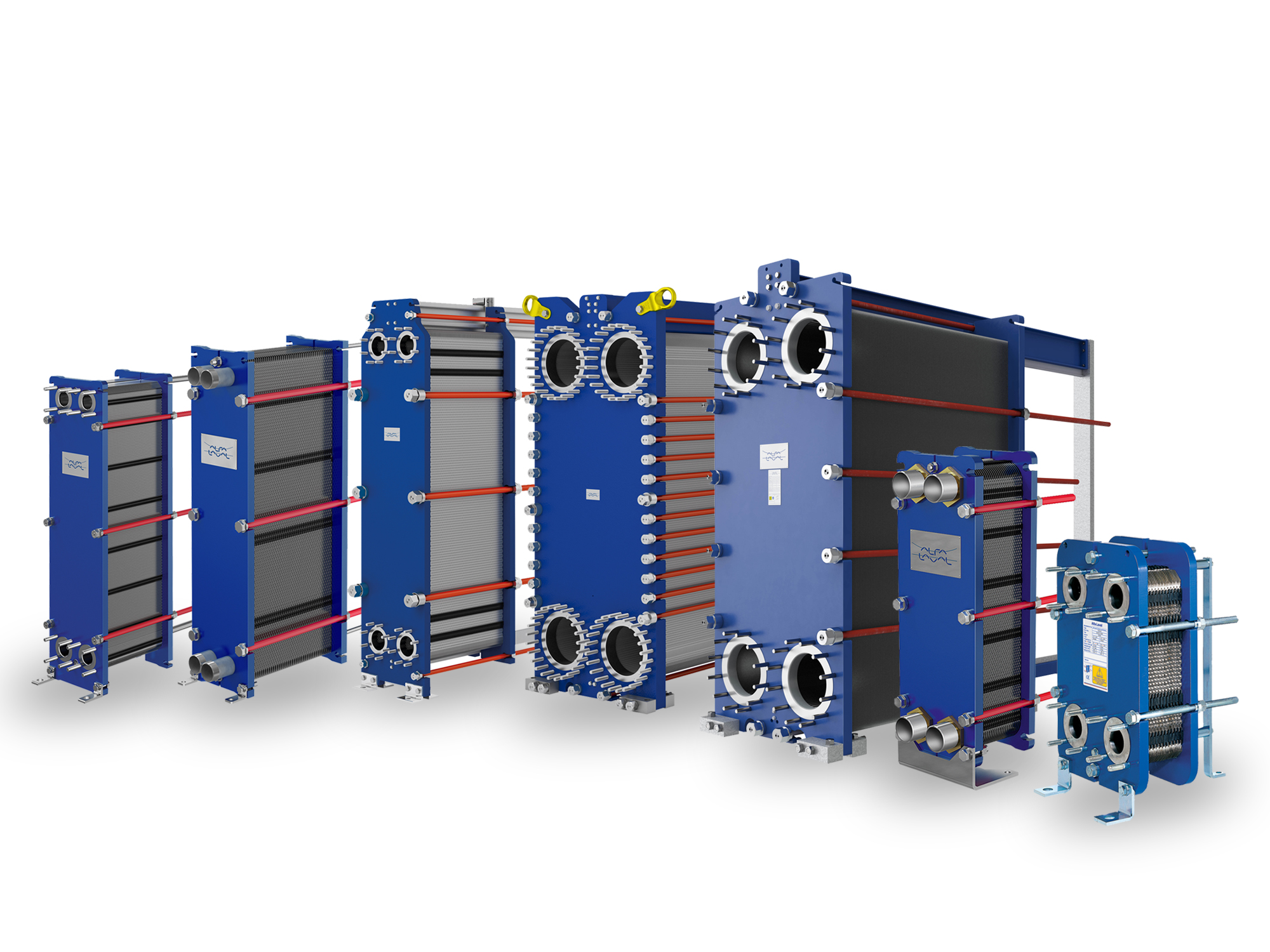
Towards new standards in efficiency, reliability and serviceability
- High energy efficiency
- Flexible – configurable for broad range of applications
- Ensures optimal performance in specific applications based on specific needs
- Easy to install
- High serviceability
Our industrial plate heat exchangers are energy efficient, compact, simple to maintain, easy to adjust for capacity changes and represent a relatively low capital investment. The vast range of options when it comes to size, plate and gasket material and add-ons means they can be specifically designed and configured for your application, from the simplest of duties to the most demanding where requirements on both performance and documentation are high.
Documents
How it works
The heat transfer area of a gasketed plate heat exchanger consists of a series of corrugated plates, assembled between a frame and pressure plates to retain pressure. Gaskets act as seals between the plates. Fluids normally run counter-currently through the heat exchanger. This gives the most efficient thermal performance and enables a very close temperature approach, ie the temperature difference between the exiting process medium and the entering service medium.
Features that make the difference
The Industrial line is equipped with features that turn this high-performance family into efficient and reliable workhorses that are easy to service and maintain over the whole product lifecycle.
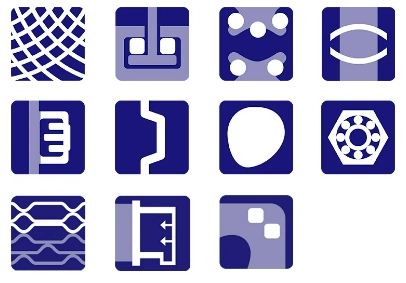
For efficiency
By improving the efficiency of your heat exchanger, you can maximize production and minimize energy consumption to reduce your power bill and improve your environmental footprint.
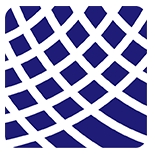
CurveFlow™
distribution area
Improves media flow and minimizes risk of fouling.
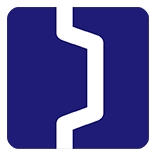
Offset gasket groove
Ensures plate utilization for maximum heat transfer efficiency.
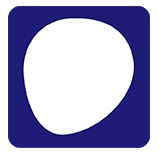
OmegaPort™
noncircular port holes
Enhances media flow and thermal efficiency.
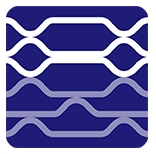
FlexFlow™
plate design
Improves thermal efficiency and optimizes pressure drop utilization.
For reliability
We are always looking to increase the reliability of every aspect of our gasketed plate heat exchangers. We focus on durable designs based on robust materials and safe manufacturing processes.
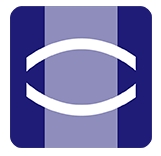
PowerArc™
plate pattern divider
Improves plate rigidity for longer lifetime.
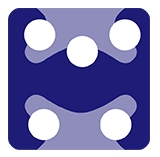
Five-point alignment
Ensures reliable plate positioning and easy to service for large units.
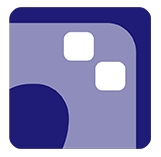
SteerLock™
plate alignment
Ensures reliable plate positioning and easy service.
For serviceability
The simple opening and closing of the plate-and-frame design with gaskets enables hassle-free inspection and service. It also enables you to easily adapt the unit to new process conditions.

ClipGrip™
gasket attachment
Ensures perfect seal and trouble-free maintenance.
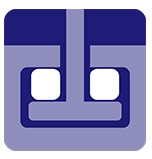
T-bar roller
Provides a lower unit that is easy to service.
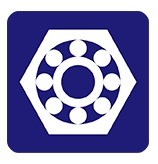
Bearing boxes
Guarantees an easy-to-open unit for smoother, more efficient maintenance.
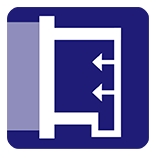
Compact frame
Facilitates maintenance and minimizes service area requirement.
Discover more features
There are many more features in an Alfa Laval gasketed heat exchanger that make a difference. New innovations and proven concepts together offer extensive benefits such as low total product life cycle cost, increased production output, minimized downtime and increased staff safety.
See the product leaflets to find the full list of features of each model in the Industrial range.
Different plates for different industrial needs
Plates are available with various pressing depths, angles of chevron pattern and various corrugation shapes, which are all carefully designed and selected to achieve optimal performance. Our Industrial line is available with four main plate configurations:
- Single plate with chevron pattern for parallel flow for optimum thermal performance and pressure drop.
- Single plate with chevron pattern for diagonal flow for optimum thermal performance when mounted horizontally and complete drainability is required.
- Double-wall plate when you need to avoid mixing fluids.
- Gemini double-wall plate when you need to avoid mixing fluids in hygienic applications.
The distribution area ensures that fluids are evenly distributed to the heat transfer area and helps avoid stagnant zones that may cause fouling.
There are a number of design features that help maximize heat transfer. The high efficiency per m2 minimizes the number of plates and the raw material used. This results in a compact, space-saving unit.
While high flow turbulence between plates results in higher heat transfer, the consequence is pressure drop. Our thermal design engineers can help you select the model and configure to what is suitable for your application so that it delivers maximum thermal performance with minimum pressure drop.
The gaskets are used to efficiently seal the heat exchanger. The gasket profile, width, thickness, type and compound of polymer are configured to each heat exchanger and its intended duty. Depending on application and frequency of unit openings, the gasket is either fastened by its clips or fingers or glued to the plate. We use a specially developed two-component cured epoxy glue for maximum adhesion in applications where frequent cleaning is necessary.